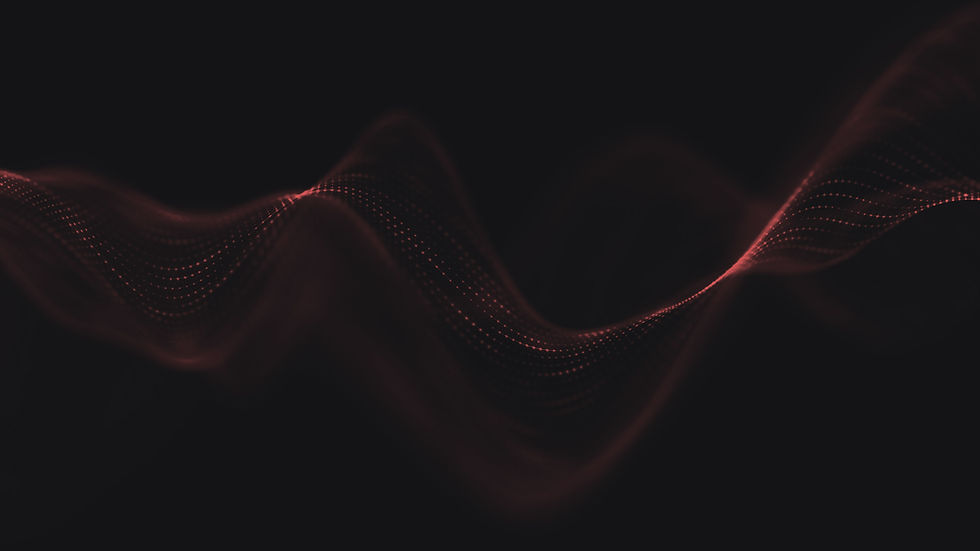
Kits
Here at Keiki Engineering Kits we help educate our community using kits. This page has all of our current available kits, as well as displaying some that are currently being developed and tested, and elaborates on our design process.
Available Kits
-
3-Axis Arm Kit
-
Manual Transmission Kit
-
Jet Engine Kit
-
7-Segment Display Kit
Kits Coming Soon
-
Contra-Rotating Propeller Kit
-
Sustainable Communities Kit
Building A Kit
Ideation
While the finished kits may look complete, and relatively simple to design, developing them takes considerable effort and thought.
Kit design starts with identifying an interesting idea or concept in the engineering space. We sit down, and just spew out different engineering concepts and ideas until something sticks.
Next, we spend some more time ideating, this time thinking about how we can possibly turn this into a kit which is straightforward and easy to understand.
After we have established exactly what we want to design, we then move to the actual design process.
Once we move into the design phase, we start by booting up a Computer Aided Design (CAD) software. For this, we use the online based CAD program OnShape - there are other popular choices, such as Fusion 360 or Solidworks.
Once in the CAD, we then create a master design/sketch that includes all the major components of the kit.
After we have a designated master sketch, we then start designing the individual components, modeling gears, mounts, servos, shafts, and all the other parts of the kit.
Design Process
Prototyping
After we've created an initial design, we start prototyping our kits. This is done via 3D printing, which allows for rapid production and iteration on our products.
We have to also order any parts that are not on hand, but are necessary for testing of the kit. This often includes different types of bearings, servos, screws, and many other miscellaneous parts that we cannot 3D print.
After the parts arrive (which is usually after 3-4 days), and all of the necessary 3D printed parts are finished, we finally start building our first version of the kit.
As is expected for every engineering process, designs for kits never work the first time around. Whether it be a major structural oversight, or a minor design flaw, there is always something wrong with the first version, or iteration, of a kit.
Iteration is an essential part of designing a kit, and is a crucial part of the overall engineering design process. When producing a kit, we will often go through anywhere between 3 and 10 different iterations depending on the complexity of the design.
Iteration
Building A Manual
After we have completed the required iteration, and have a kit that we are happy with, we then have to start building the hard part - the instruction manual.
The instruction manual isn't just instructions for assembly - it also includes simple breakdowns of important engineering concepts present in the kits.
We start by making clear instructions for the user to follow, color coding parts, and clearly designating places for parts to be inserted.
After that, we then identify appropriate spots in the assembly instructions, and insert the different breakdowns of the important concepts.
Testing the manuals is the final step in building a manual. As both of us here at Keiki Engineering Kits are somewhat experienced in engineering, we often make oversights about what is common knowledge, and make leaps about what is commonly understood.
To combat these assumptions that we make, we have family and friends who are not experienced in engineering come and test our kits and come and take a look at the manual for themselves.
If they can understand the manual, and put together the kit, we think that it is ready for the market. If not, we take their feedback, and return to the process of reconstructing the manual.
Once we've completed all of the steps above, we then have a completed kit. We record a video detailing how to assemble it in a more in-depth manner, and send off our manuals to be printed.
We then start producing our kits using 3D printing, making the parts out of PLA filament (polylactic acid), which is biodegradable*.
*Under certain conditions